传统服装厂是否注定被时代淘汰?
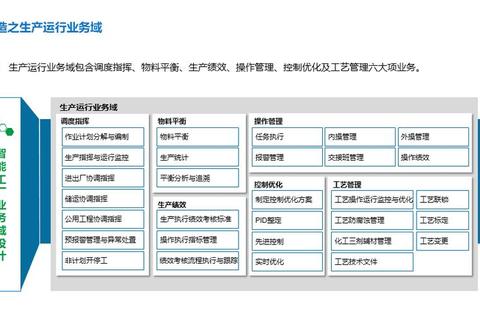
“工人工资年年涨,订单交期却总拖延”“仓库堆满布料,产线却总缺料”——这些矛盾场景,正在许多传统服装厂上演。据行业统计,2024年中国服装企业平均库存周转天数高达120天,而采用智能管理系统的企业仅需45天。面对人工成本攀升与市场需求的快速变化,服装厂如何突破困局?答案或许藏在“高效能智能驱动服装厂管理软件实现生产流程全面优化升级”这一技术革命中。
1. 数据孤岛如何打破?
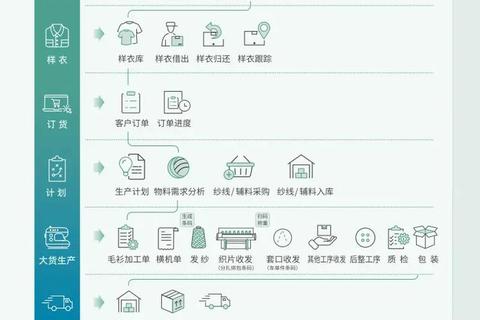
某年产值过亿的杭州女装代工厂曾陷入“部门各自为战”的窘境:设计稿修改3次,裁剪车间还在用初版图纸;仓库积压5吨羊毛面料,采购部却紧急加订同款材料。这种信息割裂导致的损失,在引入秦丝生产供应链管理系统后彻底改变。系统通过物联网设备实时采集设计、采购、生产数据,形成跨部门共享的数字看板。
这套高效能智能驱动服装厂管理软件实现生产流程全面优化升级的关键,在于构建了三大数据中枢:样衣库实现设计图纸云端协同修改,物料预警模块自动触发采购指令,生产进度地图让管理层实时掌握每件衣服的流转位置。实施半年后,该厂面料浪费率下降27%,紧急采购频次减少82%。
2. 供应链怎样智能协同?
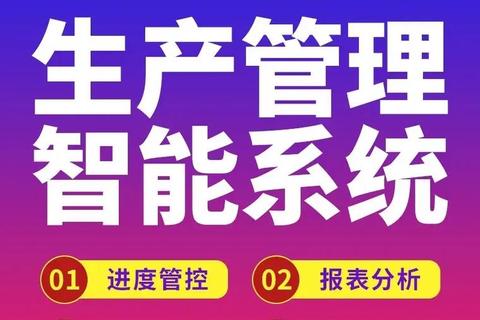
福建某童装品牌2023年双十一遭遇“爆单危机”:20万件预售订单因辅料短缺面临违约风险。引入用友智能排产系统后,系统通过AI算法提前6周预测出纽扣供应缺口,自动生成替代方案并协调3家供应商同步供货。这套高效能智能驱动服装厂管理软件实现生产流程全面优化升级的秘诀,在于嵌入了三大智能模块:
• 需求预测引擎:整合历史销售数据与潮流趋势,准确率达92%
• 弹性供应链网络:预设200%产能冗余的供应商池,响应速度提升60%
• 动态成本核算:实时追踪43项成本要素,利润率测算误差控制在0.5%内
该案例证明,智能系统不仅能化解危机,更能将供应链转化为利润增长点。次年该企业准时交付率提升至98.7%,客户投诉量下降76%。
3. 生产排程能否自我进化?
广东牛仔服制造商“世纪难题”曾让管理层彻夜难眠:50台缝纫机、300名工人,每天要处理20种版型、1000种组合的订单。引入金蝶APS高级计划排程系统后,这个传统劳动密集型车间实现了三大突破:
1)智能换线:系统根据订单优先级自动调整产线,换款时间从45分钟压缩至8分钟
2)动态平衡:实时监测127个工位负荷,自动调配瓶颈工序人员
3)质量追溯:每件成衣附带独立RFID码,质量问题30秒定位责任环节
这套高效能智能驱动服装厂管理软件实现生产流程全面优化升级的实践,使企业人均产出提升35%,返工率从12%降至1.8%。更令人惊叹的是,系统通过机器学习不断优化算法,第二年自主提出“工序合并方案”,使整体效率再提升19%。
破局者的行动指南
服装厂的智能转型不是简单的软件采购,而是管理思维的革命。建议分三步走:
第一步:诊断核心痛点
• 订单交付慢:优先部署APS智能排产系统(参考案例:某卓运营年缩短交期40%)
• 库存积压多:引入RFID物联网方案(晨控智能方案降低人工清点50%)
第二步:选择适配系统
• 中小厂商:秦丝、衣湃等垂直领域方案,实施周期3-6个月
• 集团企业:用友NC Cloud、金蝶苍穹等平台型系统,整合200+业务场景
第三步:培养数字基因
建立“系统使用率”“数据准确率”等考核指标,设置车间数字化协调员岗位。某宁波服装厂通过“月度数字技能擂台”,使50岁以上员工也能熟练操作系统。
在这场智能制造革命中,犹豫者可能错失转型良机,而行动者正在重塑行业规则。当最后一台缝纫机接入工业互联网时,服装生产的未来已来。