工业自动化中的“颜值”与“效率”之争:为何我们需要重新认识组态软件?
在传统工业场景中,工程师常面临一个矛盾:组态软件功能强大,但操作界面却饱受“界面简陋”“交互生硬”的诟病。数据显示,超过60%的操作员认为复杂的HMI界面增加了误操作风险。这种“功能优先”的设计理念是否正在成为工业效率提升的绊脚石?西门子WinCC作为全球领先的工业组态软件,正通过智能化革新打破这一僵局,高效智能掌控西门子组态软件WinCC全面赋能工业自动化,究竟如何实现“功能”与“体验”的双赢?
一、界面设计是否阻碍了工业效率提升?
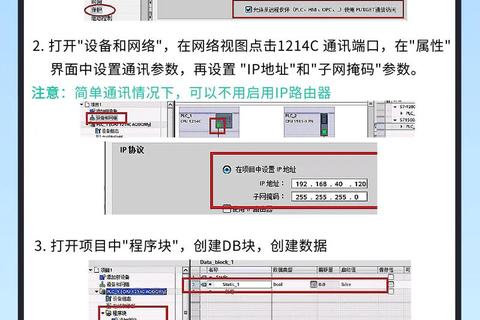
传统工控界面常以密集的数据表格和单调的指示灯为主,例如某汽车制造厂曾因报警信息混杂导致停机时间延长15%。而WinCC通过动态可视化技术彻底改变了这一局面。
以2025年某机械手监控系统为例,工程师利用WinCC的拖拽式图形库,将机械臂运动轨迹、压力传感器数据与3D模型结合,操作员通过颜色渐变提示设备负载状态,故障响应时间缩短40%。WinCC的响应式布局功能可自适应不同分辨率的屏幕,在移动端巡检时自动折叠次要信息,关键参数突出显示。
案例证明,高效智能掌控西门子组态软件WinCC全面赋能工业自动化,不仅提升了操作体验,更通过减少人为错误直接提升了产线稳定性。
二、数据孤岛如何被智能化打破?
工业现场常面临PLC、SCADA、MES系统数据割裂的问题。WinCC通过OPC UA协议实现跨平台集成,例如某钢铁厂将S7-1200 PLC的生产数据与WinCC的报警系统联动,实时分析轧机温度波动,使能耗降低12%。
更值得关注的是其预测性维护模块。某水处理厂利用WinCC的历史数据归档功能,建立水泵振动频率与轴承磨损的关联模型,提前7天预警故障,避免非计划停机损失超200万元。这种“数据-决策”闭环正是高效智能掌控西门子组态软件WinCC全面赋能工业自动化的核心体现。
三、工业4.0转型需要怎样的技术底座?
在智能制造趋势下,WinCC的数字孪生功能成为关键。某新能源电池厂通过WinCC搭建产线虚拟模型,实时映射物理设备的电流、温度数据,工程师在虚拟环境中测试工艺参数调整方案,使新品投产周期从6个月压缩至3个月。
其移动端解决方案支持远程监控。通过WinCC OA UI应用,工程师在平板电脑上即可查看全球多个工厂的实时数据,疫情期间某跨国企业借此实现跨国团队协作效率提升30%。这标志着工业控制从“固定工位”向“全域互联”的跨越。
从操作台到云端:WinCC的实践启示
对于企业而言,高效智能掌控西门子组态软件WinCC全面赋能工业自动化需关注三点:
1. 分层培训策略:初级人员掌握图形化编程(如脚本按钮颜色切换),高级开发者深入VBS/C脚本定制功能;
2. 兼容性规划:提前验证PLC型号与WinCC驱动匹配度,避免出现某食品厂因通信协议冲突导致数据丢失的教训;
3. 模块化部署:参考WinCC V7.5的冗余服务器架构,关键系统采用双机热备模式,确保99.99%可用性。
工业自动化的未来,正在从“功能堆砌”转向“体验驱动”。当组态软件既能保障产线稳定运行,又能让操作员“用得顺手”,这才是智能制造应有的模样。
--